Modular Machine Tool Design for Customized Manufacturing in the Low-Altitude Economy
As the global low-altitude economy advances toward a USD 2.5 trillion market with an annual growth rate of over 30%, the manufacturing sector faces unprecedented challenges:
How can we efficiently process lightweight materials like carbon fiber composites, which now account for over 60% of aircraft structures?
How do we respond to a flexible production landscape, where more than 75% of orders are small-batch and highly diversified?
The answer lies in modular machine tool innovation.
With "reconfigurable functionality" at its core, modular machine tools enable flexible assembly of standardized modules—supporting cross-scale machining from sub-millimeter parts to 5-meter structural components. This makes them ideally suited for the diverse materials, complex processes, and fast iteration cycles characteristic of low-altitude equipment manufacturing.
This article explores the value of modular machine tools from three dimensions: technical architecture, application scenarios, and customized solution development.
I. Limitations of Traditional Machine Tools in Customized Production
Traditional universal machine tools are still effective in standard part manufacturing. However, they fall short in meeting the typical requirements of the low-altitude sector—non-standard designs, structural complexity, and rapid iteration:
Poor adaptability: Traditional tools are often purpose-built, limiting the range of part types and failing to flexibly adapt to changing product structures.
High conversion costs: Tooling, control systems, and even machine structures must be overhauled when switching to new parts—leading to long downtimes and high expenses.
Unfriendly to startups: The high capital investment and long ROI cycle don't align with the low-altitude market, where many players are early-stage startups needing low entry barriers and fast prototyping.
II. The Value of Modular Machine Tool Design
At its core, a modular machine tool is a "platform + modules" system. Key functional units such as spindles, feed axes, CNC controls, clamping systems, and measuring modules are standardized and designed to be freely assembled like building blocks. This design directly addresses the top three manufacturing challenges of the low-altitude economy:
1. Flexible Configuration and Rapid Response
Modules like spindles, ATCs, cooling, and control systems can be tailored to specific part geometries;
When the processing task changes, only relevant modules need replacement—no need to change the entire machine.
2. Lower Investment Threshold
Startups can begin with a basic set of modules for core processes;
As product lines grow, additional modules can be added gradually—spreading out CAPEX over time.
3. Support for Hybrid and Flexible Manufacturing
The same platform can handle structural components, motor housings, and complex brackets;
Multimaterial and multiprocess machining is supported, maximizing equipment utilization.
4. Ready for Automation and Intelligence
Standard interfaces make it easy to integrate robotic arms, AGVs, vision systems, and measurement units;
Real-time data, process monitoring, and closed-loop compensation are also achievable.
Modularity is not just about plugging in parts—it's a system-level design strategy rooted in process demands, scalable growth, and functional granularity. It helps companies build a "manufacturing system that moves with demand."
III. Core Characteristics of the Low-Altitude Economy
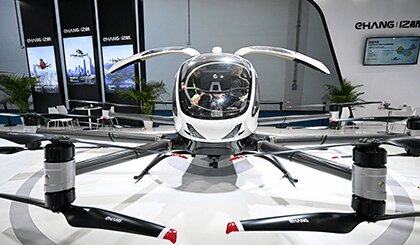
The low-altitude economy revolves around the development and utilization of airspace typically below 1000 meters, encompassing aircraft manufacturing, air mobility, and aviation services. Its manufacturing landscape has distinct features:
Product diversity: Ranges from consumer/industrial drones to eVTOLs and light helicopters
Technology intensity: Involves advanced techniques like carbon fiber machining (over 60% structural ratio), complex aerodynamic surface forming (±0.01mm), and hydrogen fuel cell bipolar plate manufacturing (±0.02mm)
Fragmented markets: Over 75% of production is small batch; product life cycles are 40% shorter than traditional industries
V. Recommended Modular Configurations for Low-Altitude Manufacturing
1. High-Speed Spindle + Multi-Axis Slide + Vacuum Fixture
Applications: UAV carbon fiber shells, eVTOL cabin skins, lightweight aluminum/magnesium parts
Highlights:
18,000–30,000 rpm spindles for high-speed lightweight material processing
Rigid 3-axis slide system for precision motion
Vacuum fixtures ensure deformation-free clamping of thin-walled parts
Value: Excellent surface quality, low thermal distortion—ideal for small-batch prototyping and precision delivery
2. 5-Axis Rotary Table + Automatic Tool Changer + Posture Compensation
Applications: eVTOL link components, composite brackets, complex housing structures
Highlights:
AC-axis rotary table for multi-surface machining in a single setup
ATC systems (16–60 tools) for varied process needs
Real-time posture monitoring and compensation for freeform surface precision
Value: Essential for high-precision, low-labor machining of complex geometry parts in both prototyping and production
3. Gantry Frame + Large-Stroke XYZ Platform + Inline Measurement
Applications: eVTOL frames, fuselage beams, cockpit doors
Highlights:
Double-drive gantry for rigidity and precision over large workpieces
Stroke >1500mm for one-piece structure machining
Inline inspection and remote monitoring for real-time accuracy control
Value: Guarantees machining consistency and alignment in large structural components before final assembly
4. Mill-Turn Compound + Rotary Axis + Automated Loading
Applications: Motor shafts, propeller hubs, transmission system parts
Highlights:
Y-axis mill-turn unit for multi-feature machining
C-axis + rotary spindle for precise angular cutting
Robotic loading system with optional dynamic balancing module
Value: Optimized for rotary parts with hybrid features; supports flexible, high-precision, scalable production
VII. Minnuo: Tailored Modular Solutions for the Low-Altitude Economy
As a solution-driven machine tool manufacturer, Minnuo focuses on real customer problems. We stay ahead of industry trends and lead the development of modular standards and scenario-specific solutions, offering platforms that are deployable, scalable, and upgrade-ready.
1. Demand-Driven Design: Starting from Your Workpiece
We reject the outdated “one-size-fits-all” approach. Our process:
Requirement analysis: Based on your part drawings, accuracy specs, and production tempo
Module recommendation: From our standard library with support for custom function tweaks
Digital validation: CAM simulation and digital twin for process verification
Scenario deployment: From module assembly to on-site commissioning, operator training, and digital process package delivery
2. Building a Core Module Library for Low-Altitude Needs
Our module R&D covers carbon fiber, titanium, 5-axis, and multi-process integration. Key modules include:
High-speed electro-spindles (24k / 30k / 36k rpm)
Vacuum clamping systems with negative pressure control
5-axis AC/BC rotary tables with <10μm precision
Expandable mill-turn turret systems
Smart units for tool changing, in-machine inspection, tool wear sensing
Thanks to standardized interfaces, over 90% of modules are interchangeable—ideal for fast deployment and long-term scalability in low-altitude manufacturing.
3. Real-World Deployment Across the Industry
Minnuo has successfully delivered customized modular solutions to numerous clients in the drone, eVTOL, and urban air mobility sectors. Sample projects include:
UAV housing and gimbal dual-process line (3-axis + vacuum table + multi-part fixtures)
Custom 5-axis centers for eVTOL structural parts (AC-axis + real-time compensation)
Batch titanium component stations (mill-turn + active measurement)
Clients report 30% shorter prototyping cycles, 70% module reuse, and sub-day product changeovers.
Conclusion
Modular machine tools are not just a product innovation—they are the strategic enabler for flexible manufacturing in the low-altitude economy.
Minnuo is not simply delivering a machine—we’re delivering a platform for intelligent aircraft manufacturing.
Contact us today to build your custom modular solution for next-generation air mobility manufacturing.