CNC Machining of Hydrogen Energy Equipment Components
With the global transformation of energy structure, could hydrogen energy become the key to the future energy revolution? As a green, renewable energy, hydrogen is gradually gaining attention from governments and businesses worldwide. Especially in fields such as transportation, energy storage, and industrial applications, the rapid development of the hydrogen industry is attracting global policy support and investment.
In the hydrogen energy industry, CNC machining technology plays a core role in the manufacturing of high-end equipment. It not only meets the high precision and complexity demands but also provides strong technical support for the precise manufacturing of hydrogen energy equipment, particularly in the production of key components such as fuel cells, hydrogen storage equipment, and hydrogen power systems.
Next, let's explore how CNC machining technology contributes to the manufacturing of hydrogen energy equipment.
1. Analysis of Hydrogen Energy Equipment Component Characteristics
Material Performance Requirements
Hydrogen energy equipment components require extremely high material performance, including excellent mechanical strength, corrosion resistance, and high-temperature resistance. Common materials include high-strength metal alloys, composite materials, and special alloys, particularly titanium alloys, aluminum alloys, and carbon fiber reinforced composites.
Application Requirements for High-Strength, Lightweight Metal Alloys (e.g., Titanium and Aluminum Alloys)
Hydrogen energy equipment typically operates under high pressure and high temperature, requiring the use of high-strength, lightweight metal alloys. Titanium and aluminum alloys are widely used in key components such as hydrogen storage, fuel cells, and high-pressure hydrogen bottles due to their light weight, high strength, and corrosion resistance.
Characteristics of Corrosion-Resistant, High-Temperature Special Composite Materials (e.g., Carbon Fiber Reinforced Composites)
Carbon fiber reinforced composites possess excellent corrosion resistance, high-temperature performance, and high strength, making them particularly suitable for hydrogen energy equipment, such as high-pressure hydrogen storage bottles and gas pipeline systems. These materials ensure the reliability and durability of equipment under extreme conditions.
Special Requirements for Hydrogen Energy Medium-Compatible Materials
As hydrogen is an extremely reactive gas, the compatibility of materials with hydrogen is a critical requirement. For hydrogen energy equipment, materials must have good hydrogen sealing properties, resistance to hydrogen embrittlement, and long-term hydrogen erosion resistance.
Structural Design Characteristics
The structural design of hydrogen energy equipment components is complex, particularly in flow channel design and precision structure machining. A rational structural design can effectively improve hydrogen flow efficiency and storage safety.
Fluid Dynamics Optimization Requirements for Complex Flow Channel Structures
Many components of hydrogen energy equipment, such as fuel cell bipolar plates and hydrogen storage bottles, often feature complex flow channel structures. These flow channels must not only account for fluid dynamics optimization but also meet the requirements for low resistance, uniformity, and flow accuracy of hydrogen flow.
Machining Challenges for Thin-Walled, Deep-Cavity Precision Structures
Many hydrogen energy components have thin-walled and deep-cavity precision structures. Machining such structures requires precise control over material thermal deformation, stress distribution, and cutting forces during the process.
High Assembly Precision Design Standards Between Components
Hydrogen energy equipment requires extremely high assembly precision between components. Even the slightest assembly errors can affect the performance and safety of the equipment. Therefore, machining precision for hydrogen energy components, particularly in hydrogen storage equipment, compressors, and key components of hydrogen refueling stations, must be exceptionally high.
Performance Parameter Standards
The performance parameters of hydrogen energy equipment encompass hydrogen pressure, flow rate, sealing properties, and pressure resistance strength, among others. The development and enforcement of these standards ensure the safety and stability of hydrogen energy equipment under various operating conditions.
2. Significant Advantages of CNC Machining in Hydrogen Power Components
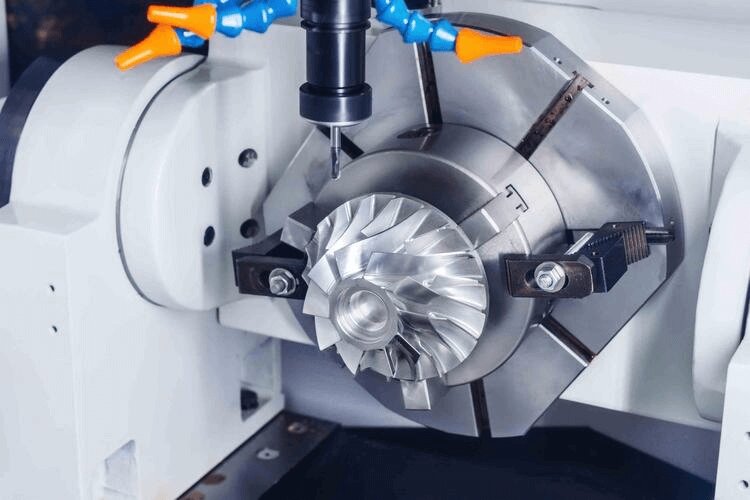
High Precision Machining Capability
CNC machining technology can achieve micron-level dimensional accuracy, meeting the precision requirements of hydrogen energy equipment. For example, the flow channels of fuel cell bipolar plates require micron-level machining precision to ensure efficient hydrogen flow.
Precise Shaping of Complex Curved Profiles
Many hydrogen energy components, such as fuel cell internal cavities and hydrogen storage bottles, require the precise machining of complex curved profiles. CNC machining technology can efficiently achieve this goal, ensuring the product meets the required airtightness and flow properties.
Efficient Production Performance
CNC machining technology is highly automated, significantly improving production efficiency. Through multi-axis linkage machining, machining time for each process is reduced, resulting in highly efficient production.
Flexible Customization Production
The design demands of hydrogen energy equipment are diverse, and CNC machining can provide flexible, customized production services based on different design requirements. This advantage is particularly suitable for the hydrogen energy industry’s small batch, multi-variety production mode.
Quality Stability Assurance
CNC machining technology offers high stability and consistency, ensuring the quality consistency of each product during batch production. Real-time monitoring and error compensation mechanisms during the machining process further guarantee product stability.
3. In-Depth Analysis of CNC Machining Key Technologies
Multi-Axis Linkage Machining Technology
Multi-axis linkage machining technology enables simultaneous movement across multiple coordinate axes, improving machining precision and efficiency. In hydrogen energy equipment manufacturing, five-axis and six-axis linkage machining are widely used in the machining of complex components.
High-Speed Milling Technology
High-speed milling can complete high-precision machining in a short time, especially for components that require high surface quality in hydrogen energy equipment. Optimized cutting parameters in high-speed milling can effectively extend tool life and reduce cutting force impact.
Precision Grinding Technology
Precision grinding processes, especially surface grinding and internal cylindrical grinding, can effectively improve surface finish and ensure the sealing properties and airtightness of hydrogen energy components.
Fusion of Specialized Machining Technologies
Electrical Discharge Machining (EDM) and laser machining technologies are widely used in the machining of hard materials and complex structures. The combination of these technologies can address specific machining requirements in hydrogen energy equipment manufacturing.
Machining Process Optimization and Simulation Technology
Finite Element Analysis (FEA) and virtual machining simulation technologies can predict potential problems during the machining process in the design stage, reducing trial-and-error costs and optimizing machining processes.
4. Diverse Applications of CNC Machining in the Hydrogen Energy Industry

Fuel Cell Core Component Machining
The manufacturing of core components of fuel cells, such as bipolar plates and Membrane Electrode Assemblies (MEA), relies on high-precision CNC machining technology to ensure good airtightness, corrosion resistance, and high conduction performance.
Hydrogen Storage Equipment Manufacturing
CNC machining is essential for processing precision components such as hydrogen storage bottle linings and hydrogen tank valve groups to ensure high pressure resistance, sealing performance, and accurate dimensional control.
Hydrogen Refueling Station Key Equipment Production
The production of key equipment for hydrogen refueling stations, such as refueling nozzle heads and pipeline connectors, requires high-precision machining and high stability. CNC machining technology provides reliable manufacturing solutions for these components.
5. MINNUO One-Stop CNC Machine Tool Solution Provider’s Technical Strength and Service Advantages
MINNUO Company Overview and Industry Position
MINNUO is a global leader in CNC machine tool solutions, specializing in providing high-precision machining equipment and technical support for the hydrogen energy industry. We are dedicated to providing precision machining solutions for fuel cells, hydrogen storage equipment, and more, ensuring the efficient and sustainable development of the hydrogen energy industry.
Comprehensive CNC Machining Equipment Matrix
MINNUO offers a full range of CNC machining equipment, including:
• Five-Axis Linkage Machining Centers: For precision component machining, ensuring high accuracy in complex surfaces and flow channels.
• High-Speed Milling Equipment: Suitable for surface finishing, improving production efficiency and extending tool life.
• Precision Grinding Equipment: Ensures high surface finish and stringent dimensional requirements, suitable for high-pressure hydrogen bottles and MEA components.
Additionally, we have other high-performance machining equipment that covers a variety of machining needs and can meet the precision machining requirements of various components in the hydrogen energy industry.
Customized Solution Service System
MINNUO provides full-process technical support from design to machining, ensuring that customer-specific requirements are met. Our services include:
• Process Optimization Solutions: Based on the specific needs of hydrogen energy equipment, we provide professional process analysis and optimization to ensure high-precision machining and improve component performance, such as optimizing flow channels and sealing designs to improve hydrogen flow efficiency and pressure resistance.
• High-Precision Custom Part Production: We provide precise custom machining for complex hydrogen energy components (e.g., bipolar plates, hydrogen storage bottle linings), ensuring assembly precision, sealing performance, and long-term stability, meeting high strength and corrosion resistance requirements.
• Equipment Maintenance and Upgrades: We offer regular equipment inspection and maintenance services to ensure optimal performance. Additionally, we provide equipment technical upgrades and process improvements based on changing industry demands to ensure efficient and stable production lines.
Conclusion
CNC machining technology plays a crucial role in the manufacturing of hydrogen energy equipment. It not only improves the precision and production efficiency of equipment but also ensures the quality and stability of products. With the rapid development of the hydrogen energy industry, CNC machining technology will continue to support innovation in equipment manufacturing.
As a leading provider of CNC machine tool solutions, MINNUO is dedicated to advancing the efficient and green development of the hydrogen energy industry. Contact us to get exclusive solutions and take your hydrogen energy equipment manufacturing to the next level in precision and efficiency!