What is Step Turning? Understanding the Process, Applications, and Key Considerations
In the manufacturing industry, how can multiple different diameters be precisely machined on the same workpiece?This challenge is likely a common headache for you. Step Turning technology is the solution, offering precise machining of step-shaped surfaces and meeting the needs for high-precision, multi-diameter components.
Step Turning works by precisely controlling the tool’s axial and radial position, cutting different diameters step by step as the workpiece rotates. This makes it highly effective and precise for machining complex parts in industries such as automotive and aerospace.
This article will explore the machining process, technical advantages, disadvantages, and analyze its applications across industries, helping you gain a comprehensive understanding of the important role this technology plays in modern manufacturing.
1. Definition and Basic Principles of Step Turning
Core Definition:
Step Turning, is a technique that involves precisely controlling the axial and radial position of the tool to cut the workpiece as it rotates. It allows for machining step-shaped surfaces on the workpiece, commonly used for shaft-type components that require different diameters.Basic Principle:
2. Step Turning Machining Process Breakdown
Pre-machining Preparation:
Workpiece Selection and Clamping Tips:
Before machining, it is essential to secure the workpiece firmly. This is the first step in ensuring precision. If the workpiece is not properly clamped, vibrations and deviations will affect the machining results. Often, slightly adjusting the clamping method can solve this issue. For precision parts, using a 3-jaw chuck or specialized fixture will provide more stability.Tool Selection Standards:
It’s crucial to select the appropriate tool based on the hardness of the material. For harder materials such as stainless steel, carbide tools are more effective, while for softer materials, high-speed steel tools may be a better choice. The shape and angle of the tool also impact cutting performance, so these factors should not be overlooked.Machine Parameter Settings:
When setting machine parameters, it’s critical to choose the correct cutting speed, feed rate, and cutting depth.For softer materials, higher cutting speeds help reduce machining time, while for harder materials, lower speeds and higher feed rates are needed to prevent excessive tool wear.Machining Steps:
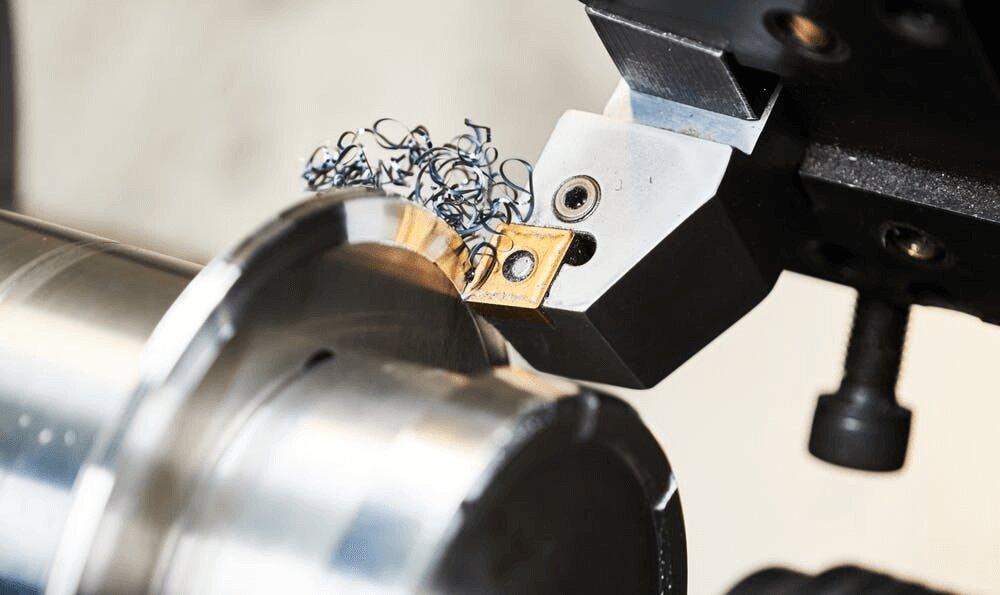
Tool Insertion Operations:
When the tool enters the workpiece, ensure the cutting angle is correct to avoid uneven surfaces. Be cautious with the depth of cut to avoid over-cutting, tool breakage, or unnecessary waste. It’s typically recommended to gradually increase the depth of cut, removing material layer by layer for better results.Step Cutting Process:
After completing each step, ensure that the tool retracts to prevent over-cutting the previously machined portion and to maintain a smooth surface. Different materials require varying levels of tool wear resistance, so adjust the retracting speed and depth according to the specific situation.3. Significant Technical Advantages of Step Turning
High Precision Machining Capability:
Step Turning can achieve micron-level precision by precisely controlling the tool path, which is crucial in aerospace or electronic device manufacturing. By optimizing the cutting process, the dimensional accuracy and surface quality of components can be significantly improved. If you’re working with particularly precise parts, ensure that each cutting step is carefully checked to avoid quality issues caused by minor deviations.High Production Efficiency:
By reducing unnecessary machining steps and shortening machining cycles, Step Turning is an ideal choice for improving production efficiency. In mass production, it can effectively increase output, especially for precision components. For example, by adjusting feed rate and cutting depth, you can significantly reduce machining time per part without sacrificing quality. MINNUO’s machine tool systems use intelligent control, making the process more efficient and ensuring stability and high efficiency in large-scale production.Wide Material Adaptability:
Step Turning is not limited to metal materials; it also works for plastics, wood, and other materials. Depending on the material, adjusting cutting parameters and tool types can achieve optimal results on materials with varying hardness and toughness. If you are processing particularly soft or hard materials, remember to adjust the machine parameters to avoid premature tool wear.4. Disadvantages of Step Turning
Material Waste:
When there are significant diameter differences between steps, more material may be wasted. For expensive materials, try to optimize cutting depth and path to reduce waste.Shape Limitations:
Although Step Turning excels in multi-diameter part machining, it may require combining other machining processes for complex non-rotational shapes. This requires flexible selection of cutting methods during operation.5. Diverse Applications of Step Turning in Various Industries
Automotive Manufacturing:
Step Turning is widely used in the manufacture of automotive components, especially in the machining of engine shafts and transmission gear shafts. These parts usually require different diameter designs, and Step Turning can precisely complete such complex multi-diameter machining tasks.Aerospace Industry:
In the aerospace sector, Step Turning ensures that components meet strict precision standards. For example, in the machining of aircraft engine blades, it is crucial to guarantee the precision of each step to ensure the reliability of parts under high temperature and pressure.Electronic Equipment Manufacturing:
With the miniaturization and precision of electronic devices, Step Turning plays a critical role in the production of micro motor shafts, connectors, and other parts. Its precision machining allows these devices to be smaller and more reliable.6. Differences Between Step Turning and Other Turning Methods
Compared to Straight Turning:
Straight turning is mainly used to machine shafts with constant diameters, with the tool cutting in a straight line along the axis of the workpiece. Step Turning, on the other hand, allows for machining multiple different diameters on the same workpiece, ensuring precision and fit for complex parts.Compared to Taper Turning:
Taper turning is used to machine parts with gradually changing diameters, where the tool reduces the cutting diameter along the axis. Step Turning, however, provides vertical diameter changes, which is crucial for parts requiring high precision and multiple positioning, such as automotive transmission shafts and aerospace engine shafts.Compared to Other Turning Methods:
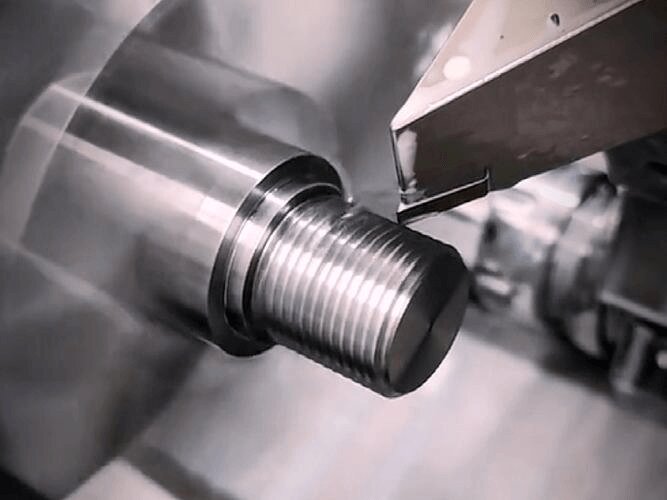
7. Materials Suitable for Step Turning
Metal Materials:
Step Turning is highly suitable for machining metal materials such as stainless steel, low carbon steel, and medium carbon steel, which are widely used in shaft component manufacturing. The corrosion resistance of stainless steel makes it particularly popular for manufacturing durable parts, but for such hard materials, carbide tools are needed for better efficiency.
Plastic Materials:
Plastics such as PTFE (Teflon) can also be machined using Step Turning, especially for parts requiring low friction. Be sure to adjust the cutting speed when machining these materials to avoid excessive heat buildup.
8. Key Factors Affecting Step Turning Machining Quality
Tool Selection and Wear Management:
The material and shape of the tool determine the cutting effectiveness. Regular inspection and timely replacement of tools are essential for maintaining machining accuracy. If tool wear is noticed, it should be replaced promptly to prevent degradation of the surface quality and precision.
Cutting Parameter Optimization:
Reasonably adjusting cutting speed, feed rate, and cutting depth can significantly improve machining quality. Too high a feed rate may lead to rough surfaces, while too low a feed rate can waste time and affect production efficiency.
Conclusion
Step Turning technology is widely applied in various industries due to its high precision and efficiency. By optimizing tools, cutting parameters, and processes, it significantly enhances production efficiency and component quality. As smart manufacturing develops, Step Turning is expected to integrate with automation technologies, further improving machining precision and efficiency.
As a professional machine tool manufacturer,MINNUO offers high-precision machines and customized solutions to meet various complex component machining needs. If you would like to learn more or receive a personalized solution, feel free to contact us. MINNUO will provide professional technical support to help improve your production efficiency and quality.