What is a Centerless Grinding Machine: Everything You Need to Know
How do manufacturers handle long, slender parts that are difficult to clamp and rotate with traditional methods? The answer lies in centerless grinding machines—a revolutionary approach that eliminates the need for center holes or chucks and delivers unparalleled efficiency in high-precision machining.
Centerless grinding machines have become essential tools in modern manufacturing, especially for mass production and precision machining of cylindrical components.
In this article, we’ll take a deep dive into what centerless grinding is, how it works, its main types, advantages, limitations, and how to choose the right machine for your needs.
Definition: What is a Centerless Grinding Machine?
A centerless grinding machine is a type of grinding equipment that grinds the outer surface of cylindrical workpieces without requiring them to be mounted between centers. Instead of clamping the part, it relies on three key components:
Grinding Wheel – Removes material from the surface to create the desired geometry and finish.
Regulating Wheel – Controls the rotational speed and axial movement of the workpiece.
Work Rest Blade – Supports the workpiece during grinding and helps maintain its position.
These components work in unison to allow continuous or plunge grinding without requiring extensive workpiece setup.
Working Principle of Centerless Grinding
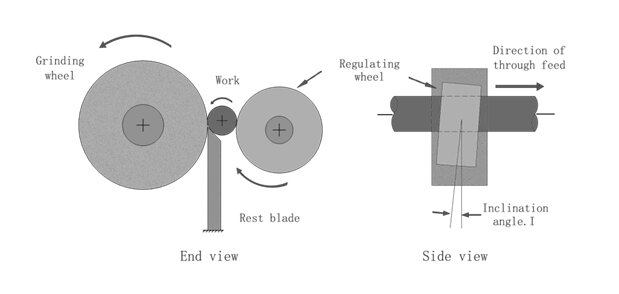
In a centerless grinding setup, the grinding wheel rotates at high speed, while the regulating wheel turns more slowly, rotating the workpiece and feeding it axially. The work rest blade sits beneath the workpiece, keeping it stable throughout the operation.
There are two main methods:
Through-Feed Grinding: The workpiece continuously passes between the wheels. Ideal for straight, cylindrical parts such as pins, shafts, and rollers.
In-Feed (Plunge) Grinding: The workpiece is fed manually and ground in place. Suitable for complex shapes or stepped components.
End-Feed Grinding:
The workpiece is fed axially from one end and ground until a specific stop is reached. Ideal for tapered workpieces or components with defined end surfaces.
Key Components of a Centerless Grinder
Machine Bed: Provides the foundation and structural rigidity; vibration-resistant beds ensure higher stability and precision.
Grinding Head: Hydraulic-controlled movement for rapid in-feed and out-feed.
Spindle System: Driven by independent motors, ensuring high-speed performance and minimal heat buildup.
Lubrication & Cooling: Essential for maintaining accuracy and reducing wear on both the wheel and workpiece.
Types of Centerless Grinding
Centerless grinders are classified based on how the workpiece is fed:
✅ Through-Feed Centerless Grinding
Workpiece moves linearly and continuously.
Best for mass production of cylindrical parts.
Used in grinding needle rollers, shafts, and bearing races.
✅ In-Feed Centerless Grinding
The part is fed manually and remains stationary during grinding.
Ideal for parts with complex shapes such as shoulders or tapers.
✅ End-Feed Centerless Grinding
Workpiece enters axially and stops against a fixed stop.
Suitable for parts with tapered or conical shapes and longer end faces.
Advantages of Centerless Grinding
High Efficiency: Continuous feeding allows rapid processing and high throughput.
No Need for Center Holes: Saves time and simplifies automation, especially in mass production.
Superior Rigidity: The combination of the regulating wheel and support blade provides greater stability than tailstock-based systems.
Improved Surface Quality: Fewer setup movements reduce vibration and inconsistencies.
Greater Material Removal: Wide grinding wheels allow deeper cuts, making the process more productive.
Disadvantages of Centerless Grinding
Limited Control Over Geometry: Difficult to maintain relative position between ground and non-ground surfaces (e.g., coaxiality).
Polygonal Roundness Issues: Poor setup or wheel condition can create odd-numbered polygons instead of perfect circles.
Complex Setup: Requires adjustment of bracket height, feed angles, and wheel positions when changing workpiece dimensions—less ideal for small-batch or prototyping.
Less Suitable for Discontinuous Surfaces: Can struggle with slots, grooves, or parts with variable diameters.
Centerless vs. Cylindrical Grinding

Feature | Centerless Grinding | Cylindrical Grinding |
Clamping | No need for centers or chucks | Requires center holes or clamping |
Speed | Higher throughput | Slower, more setup |
Precision | Excellent for roundness | Better for multi-surface geometries |
Workpiece Shape | Ideal for long rods and bars | Better for short or stepped parts |
Flexibility | Less flexible | More adaptable for different profiles |
Applications of Centerless Grinding Machines
Centerless grinding is widely used in the production of cylindrical and tapered parts where high volume and consistent accuracy are required:
Shafts: Transmission shafts, motor shafts, clutch shafts
Bearings: Outer rings, roller bearings
Automotive Parts: Crankshafts, camshafts, rocker arms
Aerospace Components: Bearing housings, engine shafts, bushings
Medical Devices: Surgical tools, orthopedic pins, and catheters
Injection Molds: Ejector pins, mold sleeves, guide pillars
Workpiece sizes typically range from 0.8mm to 60mm in diameter, with lengths up to 1000mm or more, depending on the application.
How to Choose a Centerless Grinder
Choosing the right centerless grinding machine requires consideration of the following aspects:
✔ Bed Structure
Look for a rigid, high-strength bed with vibration-dampening qualities. A stable base improves both finish and dimensional accuracy.
✔ Spindle Performance
The spindle must support high-speed rotation with minimal thermal deformation. Prefer air or oil-lubricated precision spindles with cooling systems.
✔ Control System
An integrated and user-friendly control system ensures ease of operation and consistent output quality. Look for CNC-equipped machines for better automation.
✔ Versatility and Adjustability
If you’re processing various diameters and lengths, look for machines with fast and flexible setup options.
✔ Cost-Effectiveness
Balance between machine capability, maintenance cost, and expected productivity. Consider long-term ROI, especially for high-volume production environments.
Why Choose Minnuo Centerless Grinding Machines?
At Minnuo Machinery, we offer a complete line of centerless grinding solutions tailored to your production needs. Whether you need high-speed through-feed grinding or precision in-feed applications, Minnuo machines deliver superior performance at a cost-effective price.
✅ Precision up to 0.001mm
✅ Stable, vibration-resistant beds
✅ CNC control system with user-friendly interface
✅ Robust support for automation and high-volume production
Contact us today to learn how Minnuo can help optimize your grinding process and improve your manufacturing efficiency.