In the Era of Carbon Neutrality, How Can Chinese Machine Tool Enterprises Redefine Energy Consumption Standards?
Over 130 countries and regions worldwide have set carbon neutrality targets. China’s “Dual Carbon” strategy clearly states that the country aims to achieve carbon neutrality by 2060. As a key energy-consuming component in the manufacturing sector, machine tools account for 30%–40% of total industrial energy consumption. The reconstruction of energy consumption standards has evolved from a technical proposition to a survival imperative for enterprises.
In this context, Chinese machine tool enterprises are redefining energy standards through technological innovation—by optimizing intelligent drive systems, applying green cutting processes, upgrading power systems, and incorporating AI-driven control technologies. These initiatives enable high-precision, low-energy processing and drive the iterative upgrading of industry standards.
This article analyzes the key pathways through which Chinese machine tool companies are reshaping energy standards, drawing from current industry conditions and practical experience.
I. Root Cause Analysis: Historical Challenges and Real-World Dilemmas in Machine Tool Energy Management
(1) Chronic Issues in Traditional Manufacturing Models
Under traditional manufacturing paradigms, machine tool energy management has long suffered from the "Three Highs and Three Lows":
High idle energy losses (average standby energy accounts for 22% of total),
High design redundancy (transmission system energy loss exceeds 18%),
High operational inefficiency (60% of enterprises lack energy monitoring systems).
On the other hand:
Low awareness of energy efficiency (only 35% of companies set energy-saving KPIs),
Low data infrastructure (90% of older equipment lacks energy consumption interfaces),
Low system integration (production scheduling and energy management are disconnected).
These factors lead to China's machine tool sector consuming over 30% more energy per unit output than countries like Germany and Japan.
(2) Paradigm Shift Triggered by the Carbon Neutrality Strategy
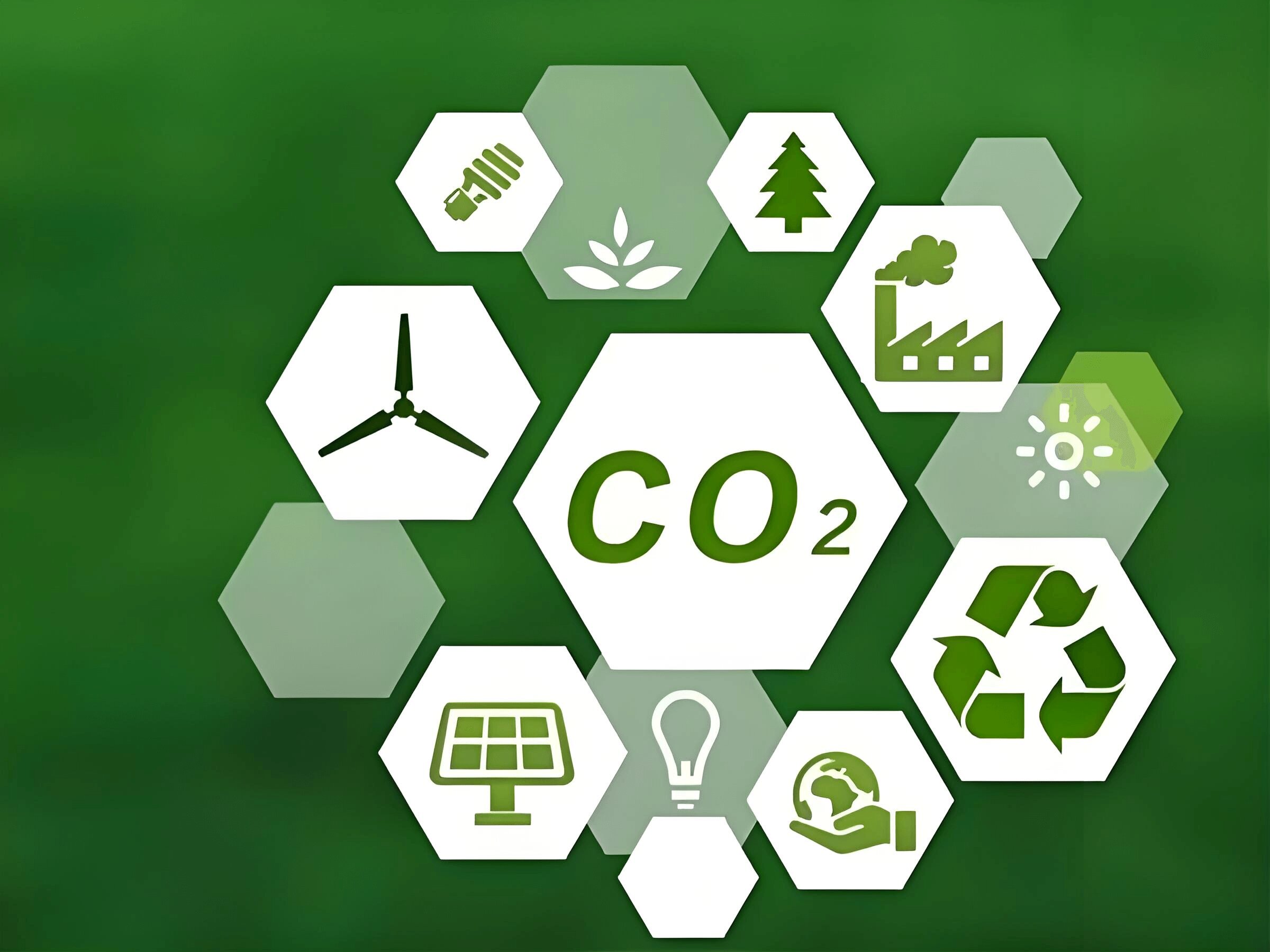
As the carbon neutrality agenda accelerates, the machine tool industry faces three disruptive transformations:
Policy Rigidity: The Industrial Sector Carbon Peak Implementation Plan mandates a 15% reduction in energy consumption per unit added value in the machine tool industry by 2025, turning energy management from a voluntary initiative into a regulatory requirement.
Cost Structure Overhaul: Pilot carbon tax schemes could increase operating costs of high-energy-consuming machine tools by 25%–40%, pushing enterprises toward energy-efficient alternatives.
Technology Architecture Upgrade: The Ministry of Industry and Information Technology's Machine Tool Energy Efficiency Enhancement Action Plan requires full energy data acquisition and networking for mainstream machine models by 2027.
II. Strategic Pressure: “Triple Drivers” for Standard Upgrades in the Carbon Neutral Era
(1) Policy Pressure: Transition from Voluntary to Mandatory Standards
National Level: The Industrial Carbon Peak Implementation Plan promotes the evolution of GB/T 39354 Energy Efficiency Testing Method for Machine Tools from a recommended to a mandatory national standard.
International Benchmarking: The EU ERP Directive mandates standby energy consumption for machine tools to be ≤1W by 2027, urging export-oriented enterprises to prioritize energy-saving retrofits.
(2) Market Restructuring: Client Demand Shifts Toward “Low-Carbon Competitiveness”
Automotive OEMs: Now include machine tool energy efficiency as a supplier qualification metric. Volkswagen Group requires supplied machines to meet Grade II efficiency or higher and mandates integration of energy data into the factory EMS.
New Energy Industries: Sectors like photovoltaics and lithium batteries—due to 24/7 operations—demand ultra-efficient equipment, requiring per-unit processing energy consumption to be <0.8 kWh/piece (20% below traditional standards).
(3) Technological Empowerment: Intelligent Tools Redefine Evaluation Systems
Digital Twin Technology: Simulates energy curves under different machining processes, enabling precise process-level energy benchmarks (e.g., spindle energy use during Ti-6Al—4V machining is reduced).
Blockchain Traceability: A leading machine tool group has piloted blockchain-based energy data certification, supporting carbon footprint audits and green manufacturing certification.
III. The Breakthrough Path: A Three-Dimensional Approach to New Energy Standards
(1) Technological Innovation: Global Giants Leading the Way
In response to the demands of the carbon neutrality era, machine tool leaders in Europe, the U.S., and Japan are pioneering breakthroughs in energy-saving technologies:
Haas Automation (USA): Targeting North America’s automotive component market, Haas launched its VF series of energy-efficient vertical machining centers. These use direct-drive motors combined with harmonic reducers to reduce energy loss in the transmission chain. Composite lubrication reduces guide rail friction by 35%, cutting overall energy use by 22% compared to previous models.
Mazak (Japan): In its Integrex i series, Mazak incorporates thermally symmetrical design and intelligent thermal displacement compensation to minimize energy loss caused by heat deformation, lowering multi-task machining energy use by 18%.
Meanwhile, Chinese enterprises are catching up quickly:
Shenyang Machine Tool: Leveraging its i5 smart platform, it developed a new generation of high-speed precision CNC lathes featuring a proprietary dual-drive backlash elimination system and high-precision grating feedback, boosting positioning accuracy to ±0.002mm. Simultaneously, energy use during cutting was reduced by 18%. Integrated energy recovery modules convert braking energy into reusable power.
Dalian Machine Tool: Targeting aerospace needs, Dalian created a specialized gantry machining center for difficult-to-machine materials. The use of hydrostatic spindle bearings increased rotational precision to 0.5μm. Coupled with minimum quantity lubrication (MQL), cutting fluid usage dropped by 95%, and processing energy use fell by 15%.
From time-honored global leaders to China’s rising pioneers, innovation in machine tool energy efficiency continues at pace. As a transformative force in the sector, Minnuo is redefining the standard with a next-generation technological matrix.
(2) Minnuo Technology: Redefining Industry Energy-Efficiency Benchmarks
As a solution-oriented machine tool manufacturer, Minnuo is building a comprehensive energy-saving system driven by Technology + Data + Service:
Hardware Layer:
Ultra-Precision Transmission: The EcoMaster series employs nano-grade ceramic bearings with a friction coefficient as low as 0.0008. Coupled with intelligent temperature control, high-speed operation energy is reduced by 12%. Self-developed dual cycloidal gear reducers offer 98% transmission efficiency, lowering energy loss by 15% versus traditional gearboxes.
Smart Energy Management System: Integrated regenerative braking modules store braking energy for reuse in auxiliary systems. High-efficiency PMSM linear motors improve drive response by 30%, reducing energy use by 20%.
Green Cutting Technology: Standardized MQL systems paired with proprietary cutting fluid formulations achieve a 95% fluid recycling rate and cut process energy use by 18%.
Data Layer:
AI Energy Prediction: The Minnuo Cloud platform uses deep learning models to analyze historical machining and equipment data, achieving over 92% accuracy in energy prediction and enabling pre-optimized process parameters.
Digital Twin Optimization: Virtual machine models simulate energy consumption under various conditions, generating optimal process parameter sets—yielding 15%–20% energy savings.
Multi-Machine Scheduling: Supports factory-level machine clusters, balancing workloads via smart scheduling algorithms to cut peak electricity demand by 25%.
Service Layer:
Smart Diagnostics & Retrofitting: For aging equipment, high-precision sensors and edge computing modules enable real-time energy monitoring. Data-driven retrofit plans—such as servo upgrades or transmission system optimization—are then deployed.
Custom Standard Development: Leveraging proprietary simulation tools, Minnuo creates tailor-made energy management standards and efficiency plans based on industry specifics and customer workflows.
IV. Outlook: Defining Future Competitiveness Through Standard Reconstruction
As energy consumption standards evolve from regulatory thresholds to value propositions, Chinese machine tool companies are presented with a historic opportunity:
Export Markets: Machines that meet EU CE-PED 2014/68/EU and US EISA energy standards can command 15%–20% price premiums.
Domestic Advantage: A new energy auto parts supplier has chosen Minnuo’s energy-saving machines, as their per-unit energy data can be directly incorporated into OEM carbon credit calculations.
The redefinition of energy standards in the carbon-neutral era is, in essence, a transformation in the logic of manufacturing—from “usable” to “efficient use,” and from “individual machine savings” to “system-wide decarbonization.” The wave has arrived. Minnuo is leading the charge in reengineering energy standards with cutting-edge technologies and customized solutions. Contact us now to begin your low-energy intelligent manufacturing journey!