How to Choose the Right Heavy Duty Lathe Machine
How to Choose the Right Heavy Duty Lathe Machine
Can't cut, can't clamp, low efficiency? It's probably not your operation that's wrong—it's the wrong lathe you've chosen.
Three things matter most when selecting a heavy duty lathe machine:
Workpiece – How big is the diameter? How hard is the material?
Process – Is it single-piece trial production or batch machining?
Workshop condition – Can your foundation, power supply, and team handle it?
These three aspects determine which type of heavy duty lathe machine you should choose.
In this article, we’ll walk you through everything you need to know to select the heavy duty lathe that truly fits your production needs.
1. Heavy Duty Lathe Types
In the machining industry, a heavy duty lathe machine refers to a robust, high-torque, high-rigidity horizontal lathe designed for continuous cutting of large-size, high-hardness metal workpieces. Based on functionality and structure, they can be classified into the following types:
● Standard Heavy Duty Lathe
Manual or conventional control, ideal for single-piece or small-batch production
Commonly used in general-purpose machine shops
Features: strong structure, simple operation, easy maintenance
● CNC Heavy Duty Lathe Machine
Equipped with CNC control system for programmable cutting paths
Suitable for repeatable machining, batch orders, and complex profiles
Features: enhanced consistency, controllable precision, automation-ready
● Double Spindle Heavy Duty Lathe
Dual spindles or dual tool post configuration
Allows simultaneous machining at both ends, suitable for symmetric long shafts or heavy rollers
Features: one-time clamping, improved concentricity, significantly reduced cycle time
● Customized Large Heavy Duty Lathe
Tailored based on customer’s specific machining processes
Includes modular options such as special tailstocks, hydraulic chucks, remote monitoring, and in-process measuring systems
Features: fully aligned with production line needs, widely used in energy equipment and defense sectors
Extended Note:
At Minnuo, our CK61 series covers all the types above and can be customized according to customer industry needs (e.g., automatic loading/unloading, high-pressure cooling, multi-process configuration).
2. How to Choose the Right Heavy Duty Lathe?
Choosing the right heavy duty lathe requires more than just comparing prices or specs. It should be a comprehensive decision based on workpiece characteristics, process requirements, and plant investment capabilities.
✅ Workpiece Requirements
If your workpiece diameter ranges from 500mm to 800mm and length reaches 2 meters or more, consider an 800mm swing heavy duty lathe.
For quenched steel or high-strength alloy, select a model with high torque spindle.
High material hardness requires high power spindles.
For two-end machining, prioritize double spindle structure.
✅ Process & Production Demand
For batch and repetitive machining: choose CNC heavy duty lathe.
For complex tool paths or multiple tool setups: ensure the machine can support turret tools or functional axes.
For high efficiency and integrated processing: consider automated loading systems or synchronized axis configurations.
✅ Investment & Facility Compatibility
Does your facility have the space, power capacity, and ground foundation for a large lathe?
Do you have a team capable of handling hoisting, programming, and CNC operations?
Are you planning future upgrades involving networking or industrial IoT integration?
Tip: We recommend selecting a lathe model with 10–20% capacity margin to accommodate future upgrades or machining challenges.
3. Typical Industry Applications
Below are common configurations of heavy duty lathes tailored to various industrial scenarios:
Industry | Typical Workpieces | Recommended Lathe Type |
Auto Components | Crankshafts, drive shafts, hub seats | CNC Heavy Duty Lathe |
Wind Power | Main shafts, shaft ends, hub flanges | Double Spindle Heavy Duty Lathe |
Construction | Drive shafts, hydraulic cylinders | Standard Heavy Duty Lathe |
Energy Equipment | Turbine shafts, high-pressure heads | Customized Large Heavy Duty Lathe |
Defense/Aerospace | High-strength alloy rings, large end caps | High-precision CNC Heavy Duty Lathe + turret |
4. Daily Maintenance & Best Practices
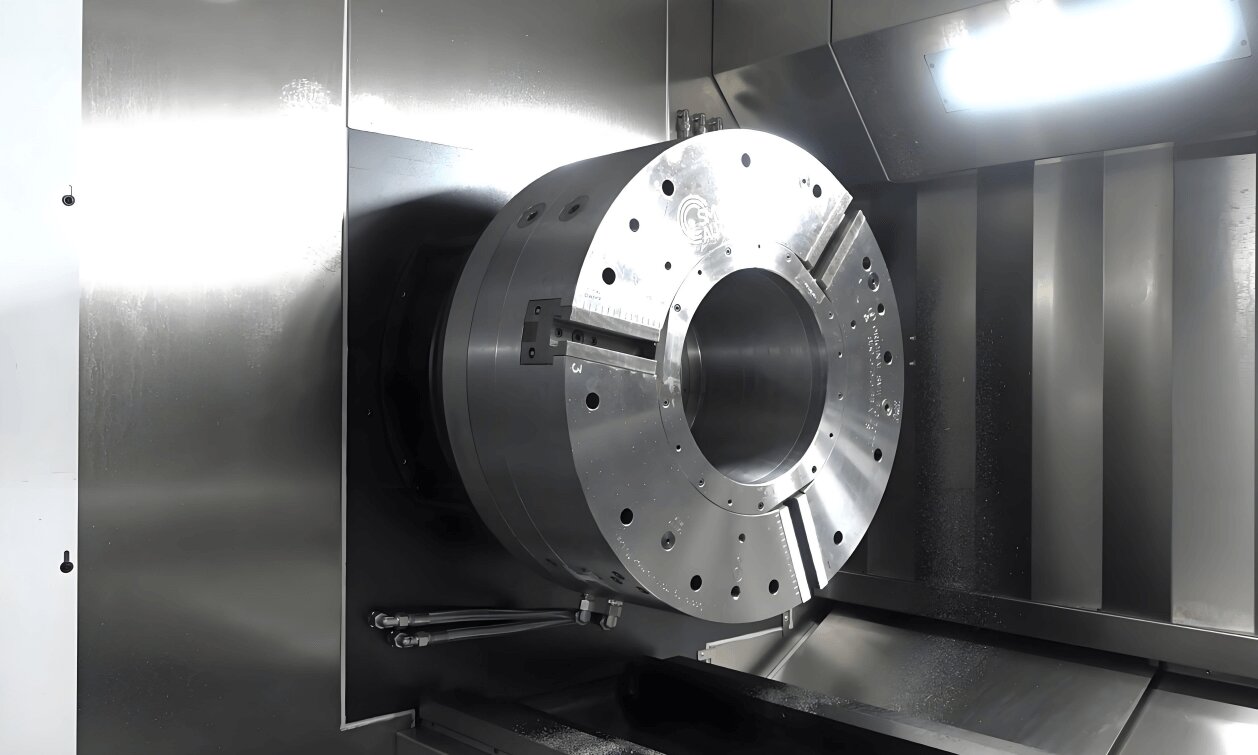
Maintenance is essential for keeping a heavy duty lathe machine running stably under high-load conditions. Here are key focus areas:
● Spindle System
Regularly monitor spindle temperature; add cooling intervals if runtime exceeds 8 hours
Always use original-grade lubricants to ensure bearing system reliability
● Bed Guideways & Feed Mechanism
Clean chip debris every shift to prevent wear
Use high-viscosity guideway oil to form protective film, slowing wear
● Electrical & CNC System
Periodically check PLCs and cable connections to avoid contact issues
Regularly back up CNC parameters to prevent unexpected data loss
● Tooling System
For heavy cutting, inspect tool tips after machining a certain length
Regularly calibrate tool post locking torque to avoid looseness, deformation, or chatter
Reminder: The earliest sign of accuracy deviation in heavy lathes usually comes from spindle thermal drift or guideway feed irregularity—develop the habit of trend monitoring.
✅ Conclusion: Make Your Lathe Work for Your Manufacturing Goals
In a sea of lathe products, choosing the right heavy duty lathe machine isn’t about stacking specs—it’s about matching it to your process, your production rhythm, and your future expansion plan.
If your workpieces are large, heavy, and hard, and you’re chasing speed, stability, and accuracy—
✅ Then you don’t need a generic lathe. You need a professional heavy duty lathe solution.
Contact Minnuo for personalized heavy duty lathe machine recommendations and detailed product manuals. We'll help you find the model that fits best—so your production line runs faster, steadier, and better.