Breakthroughs in Composite Processing Technologies for Low-Altitude Aircraft
As the global low-altitude economy expands rapidly, Joby Aviation completed the first manned transition flight of its eVTOL in April 2025, while Airbus is accelerating the development of new unmanned logistics systems. However, the industry is being held back by a high rejection rate of up to 10% in composite processing. With aircraft design iterations speeding up, how can breakthroughs in material processing technologies transform laboratory innovations into scalable production capacity?
Today, advanced Automated Fiber Placement (AFP) and Automated Tape Laying (ATL) technologies enable high-precision, automated fabrication. Thermoplastic composite molding technology has tackled the challenge of rapid curing, and new adhesive materials and bonding processes have significantly enhanced joint strength. These advances unlock tremendous potential for boosting low-altitude aircraft performance.
Want to dive deeper into how these cutting-edge technologies are reshaping the landscape of low-altitude aircraft manufacturing? Let’s explore the world of composite processing innovations.
1. What Are Low-Altitude Aircraft?
Low-altitude aircraft refer to flying vehicles operating at altitudes below 1,000 meters. These include drones, helicopters, and electric vertical takeoff and landing (eVTOL) aircraft. Widely used in logistics delivery, urban transportation, agricultural spraying, and emergency rescue, they play an increasingly important role. For example, drones can deliver supplies to remote areas, and eVTOLs promise to revolutionize urban mobility. As the low-altitude economy develops, the demand for performance, safety, and cost control continues to rise.2. Composite Materials for Low-Altitude Aircraft: Types and Characteristics
Material Type | Representative Materials | Core Properties | Processing Implications |
Fiber-Reinforced Composites | Carbon fiber, glass fiber, aramid fiber composites | High strength, low density, fatigue resistance, weak interlaminar bonding | Prone to delamination, rapid tool wear, requires specialized techniques; carbon fiber requires anti-static precautions |
Metal Matrix Composites | Aluminum- and titanium-based composites | High thermal conductivity, wear resistance, titanium resists high temperatures, aluminum causes tool sticking | Titanium is difficult to cut, requires high-performance equipment; aluminum tends to cause built-up edge |
Functional Composites | Stealth and wave-transparent materials | Stealth materials absorb waves; wave-transparent materials minimize loss, contain special fillers | Stealth composites require even distribution of absorbers; wave-transparent ones demand excellent surface finish |
These composites are essential for aircraft manufacturing due to their lightweight and high strength, but they also pose significant machining challenges, such as delamination, difficulty in metal matrix processing, and special handling needs for functional materials.
3. Challenges in Current Processing Technologies
(a) Limitations of Traditional Forming Methods
Process Type | Major Limitations | Typical Issues |
High equipment cost, long cycle time, high energy consumption | Equipment costs can exceed millions; curing cycle takes 4–8 hours with high energy usage | |
Poor quality stability | Prone to voids and delamination; unsuitable for high-precision parts | |
Compression Molding | Short mold life, unsuitable for complex surfaces | Complex mold design and resin flow inconsistency can impair part quality |
(b) Bonding and Joining Challenges
Mechanical Fastening: Stress concentration and fiber damage during drilling can reduce structural strength by 30–50%.Adhesive Bonding:
Durability is highly sensitive to environmental factors like temperature and humidity.
Demands strict surface preparation (e.g., sanding, chemical cleaning); slight missteps can severely impact joint strength.
(c) Machining and Drilling Difficulties
Defects: Delamination and burrs are common.Tool Wear: Traditional tools wear out quickly.
Precision: Hard to maintain tolerances—rough hole walls and diameter errors affect assembly and performance.
4. Breakthroughs in Advanced Processing Technologies
(a) Innovative Forming Techniques
Automated Fiber Placement (AFP) / Tape Laying (ATL):Robotic arms and dedicated programming ensure ±0.1mm laying precision, enabling accurate fiber orientation for forming complex structures like drone fuselages.
Resin Transfer Molding (RTM) and Vacuum Infusion Process (VIP):
Optimized injection equipment and mold design shorten fill time.
Improved fiber preform design boosts fiber volume fraction and mechanical performance.
Thermoplastic Composite Molding:
Rapid curing (5–30 minutes) and one-shot forming of complex shapes—ideal for crash-resistant drone parts.
(b) Advanced Bonding Innovations
Co-Curing / Co-Bonding:Enables integrated structures, reducing weight by 20–30% and improving efficiency—applied in eVTOL sandwich fuselage manufacturing.
New Adhesive Materials and Processes:
Nanoparticle-reinforced epoxy combined with plasma surface treatment increases joint strength by over 50%, solving traditional durability issues.
(c) Efficient Cutting and Drilling Methods
Specialized Tooling:Diamond-coated carbide tools and step drills extend tool life by 5–10 times and reduce delamination during exit.
Non-Traditional Machining:
Laser: Contactless cutting avoids fiber damage.
Waterjet: Abrasive waterjets efficiently process complex shapes with minimal dust.
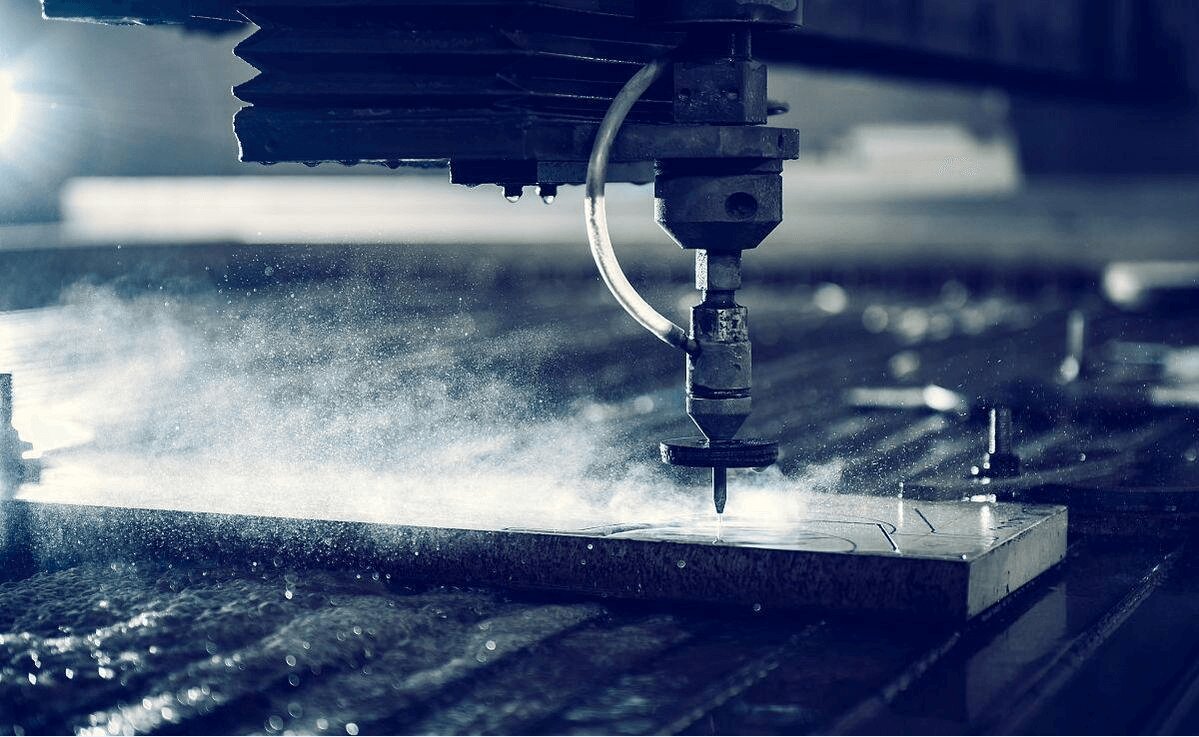
5. Industry Impact of These Breakthroughs
(a) Performance Enhancements
Extended Range and Payload:Advanced composite parts enable 30% longer drone range and 25% higher payload.
Improved Safety:
Stronger structures enhance stability and wind resistance in adverse weather.
(b) Cost Efficiency
Technology Cost Reduction Value AddedRTM Process Mold costs are 1/3 of autoclave, with shorter cycles Enables scalable mass production
Composite Parts Longer service life Reduces maintenance and lifecycle costs
(c) Application Expansion
Logistics:Efficient drones enable accurate last-mile delivery.
Urban Transport:
eVTOLs with advanced composites show high feasibility in alleviating traffic congestion.
Other Fields:
Higher spraying accuracy in agricultural drones; stronger crash resistance in emergency UAVs.
6. Challenges Ahead and Strategic Responses
(a) Technical Challenges and Solutions
Challenges:Increasing material multifunctionality and structural complexity raise processing and quality inspection difficulties.
Solutions:
Promote interdisciplinary collaboration across materials science, mechanical engineering, and computing.
Invest in cutting-edge inspection tools like high-resolution ultrasonic systems and AI-based defect detection.
(b) Industry Ecosystem Challenges and Solutions
Challenges:High costs and unstable supply of materials like carbon fiber; insufficient upgrade funds and talent shortages among manufacturers.
Solutions:
Optimize supply chains and establish material reserves; deepen supplier partnerships.
Develop talent through industry-academia collaboration and training programs.
7. Minnuo’s Innovations and Applications in Composite Processing for Low-Altitude Aircraft
Advanced Equipment Development
5-Axis Machining Center:
Driven by linear motors with a gantry frame, equipped with Renishaw calibration system. Positioning accuracy ±0.005mm, spindle speed 24,000 rpm. With ultrasonic vibration, delamination factor during carbon fiber milling ≤1.1—ideal for precision components.Special Drilling System:
Integrates visual positioning and floating drill chuck. Step-drill pecking technique with backing support achieves ±0.02mm hole tolerance and prevents delamination in layered drilling.Process Optimization
Process | Core Technologies | Application Results |
PID + fuzzy control, VARI injection | 20% faster filling, 60% fiber volume fraction, 18% higher strength | |
Composite Bonding | 300W plasma treatment + proprietary primer | Surface roughness Ra 1.2μm, bonding strength 25 MPa (30% improvement) |
Digital Technology Integration
Digital Twin Simulations:Simulation models built with ANSYS and Python reduce trial iterations by 30%.
Smart Monitoring:
Sensors collect force and vibration data. Machine learning predicts tool wear and triggers auto-replacement when exceeding 15% threshold—extends tool life by 25%, improves efficiency by 12%.
Conclusion
Breakthroughs in composite processing for low-altitude aircraft—from technological innovations to efficiency gains—are reshaping the industry landscape, though challenges persist.Ready to overcome machining hurdles and seize the low-altitude economy? Minnuo’s cutting-edge equipment and custom solutions are here to help. Contact us today to unlock the future of efficient production.